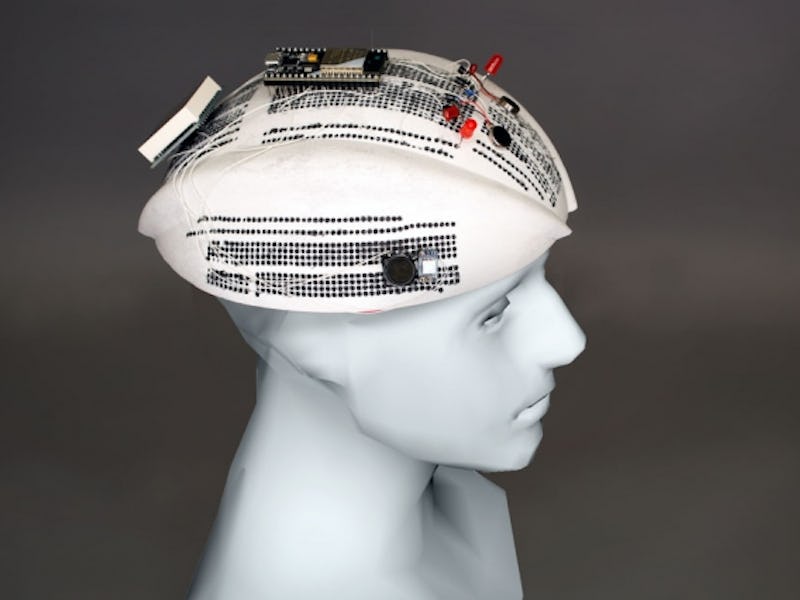
Researchers at MIT appear to have solved a problem created by our growing love of wearable computers, a current infatuation that has turned into full-on commitment for many who rely on them to track personal health data. (If your Apple Watch didn't record your workout, did it actually happen?)
Smart watches (nearly 50 million shipped last year), headphones, and e-reader sales are going up, and it's just the beginning. Smart bicycle helmets and curved appliances could be put on the market faster, if R&D could be done more efficiently.
There was just one problem.
Prototyping those tiny, curved computers is really difficult using the old-school method — plugging circuits into a rectangular "breadboard."
Look at this thing:
An old-skool, 400-socket breadboard.
This problem motivated engineers at the university's Computer Science and Artificial Intelligence Laboratory to design a highly customizable approach to designing a breadboard surface, one that allows users to have more freedom when prototyping their devices on a variety of surfaces.
Using a 3D printer, they made a CurveBoard to use when routing electronic components around 3D surfaces that are designed for durable, wearable, everyday use. (Those trips to the gym aren't going to record themselves.)
Their research is published in this study, which will be presented at the Conference on Human Factors in Computing Systems in April in Honolulu, Hawaii.
New-skool: CurveBoards are 3D breadboards — which are commonly used to prototype circuits — that can be designed by custom software, 3D printed, and directly integrated into the surface
They aren't the first to try a more flexible approach to designing breadboards, but the authors say their approach differs because users can still reposition components in real-time when testing.
"Alternative methods, such as taping the components onto the prototype, offer more flexibility; however, they make it difficult for designers to exchange and rewire parts and do not offer the same circuit building support as breadboards," they write. "Once fabricated [in other models], the circuit traces and components are fixed, i.e. none of these methods allows for high circuit fluidity."
Junyi Zhu, first author on the study and a CSAIL graduate student, says the design introduces an entirely new axis for engineers to explore-- a "function" axis.
“On breadboards, you prototype the function of a circuit. But you don’t have context of its form — how the electronics will be used in a real-world prototype environment,” said Zhu. “Our idea is to fill this gap, and merge form and function testing in very early stage of prototyping an object. … CurveBoards essentially add an additional axis to the existing [three-dimensional] XYZ axes of the object — the ‘function’ axis.”
The CurveBoards achieve this functionality in a few different ways. First, users are able to import a 3D model of the object they're prototyping, say, a smartwatch, into CurveBoard's custom software. In the software, a user can choose to generate pinholes (which will later be filled with conductive silicon) and choose the layout of the CurveBoard's connectivity channels. The design can then be exported and sent to a 3D printer.
Once printed, each pinhole is filled with conductive silicon to allow users to plug-and-play with different components of their system designs. To see just how well their CurveBoard stacked up against a traditional breadboard, the team brought in a group of six participants (three male, three female) and had them complete design tasks using both traditional breadboards and the new CurveBoard.
The authors report in the study that the participants overall had a much easier time completing the task using Curveboards than breadboards.
"I spent a lot of time with the 2D breadboards figuring out the best way to situate and attach them to the bracelet, which I didn’t have to do in the 3D breadboard use," stated one participant in the study.
That said, the Curveboards still weren't 100 percent perfect. The participants requested that the boards incorporate firmer connection points in future designs.
And despite their design's successes, the authors write that their Curveboard isn't meant to disrupt or overtake the traditional breadboard, but instead supplement it.
“People love breadboards, and there are cases where they’re fine to use,” Zhu said. “This is for when you have an idea of the final object and want to see, say, how people interact with the product. It’s easier to have a CurveBoard instead of circuits stacked on top of a physical object.”
Going forward, the team hopes to continue improving their Curveboards through incorporating ready-made templates into their software (e.g. a standard smartwatch build) so users don't have to design their prototypes from scratch each time. They also hope to move some of the physical prototyping, such as circuit testing, onto the software as well, said Zhu.
"That way you’ll know exactly how it’ll work in the real world, enabling fast prototyping,” said Zhu.
With the smartwatch market expected to approach 118 million units sold in 2025, a fix can't come soon enough.
Abstract: CurveBoards are breadboards integrated into physical objects. In contrast to traditional breadboards, CurveBoards better preserve the object’s look and feel while maintaining high circuit fluidity, which enables designers to exchange and reposition components during design iteration. Since CurveBoards are fully functional, i.e., the screens are displaying content and the buttons take user input, designers can test interactive scenarios and log interaction data on the physical prototype while still being able to make changes to the component layout and circuit design as needed. We present an interactive editor that enables users to convert 3D models into CurveBoards and discuss our fabrication technique for making CurveBoard prototypes. We also provide a technical evaluation of CurveBoard’s conductivity and durability and summarize informal user feedback.