Tesla is running up against the biggest problem in electric cars
Tesla wants to make more cars, but it can't.
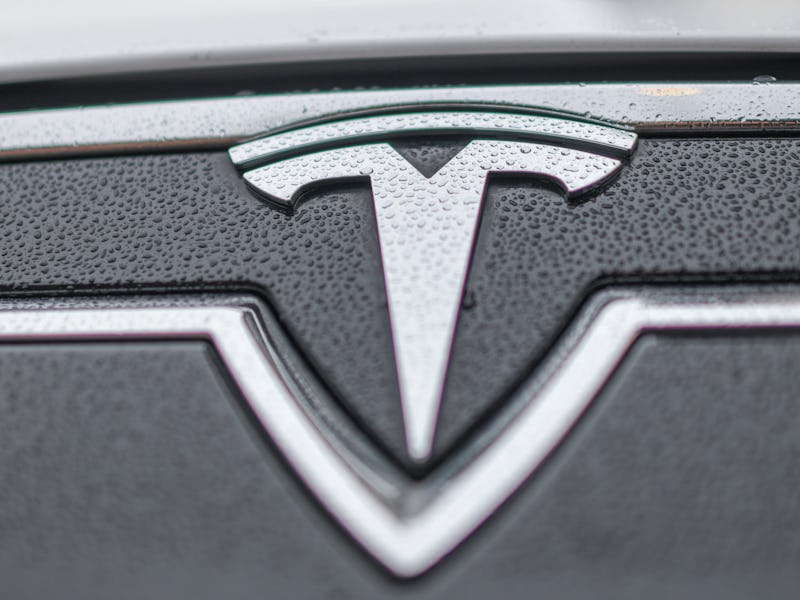
Tesla’s entire business depends on electric cars, which in turn depend on batteries. A shortage of batteries, a seemingly small bump on the road to electrification, could slow down the otherwise-accelerating leap to the future of cars.
The issue came to the forefront during Tesla’s fourth-quarter 2019 earnings call last week. CEO Elon Musk described battery production as “very fundamental and extremely difficult,” as the company struggles to transition from being a niche premium carmaker to a mass-market juggernaut. The cell-starved firm was previously forced to scale back Solar Roof production to meet car demand, and mass production for the cell-hungry Semi truck has now missed its 2019 start date as Tesla focuses on the Model 3 and Model Y mass-market cars.
So why is this happening? Is Tesla’s dependence on materials like lithium and cobalt holding back production? While lithium production surged from under 40,000 tons of lithium carbonate equivalent in 2016 to over 80,000 tons in 2018, demand for batteries has also skyrocketed during that time.
“At the moment, as far as I know, lithium supplies are not currently affecting production of lithium cells,” Maria Chavez, an energy analyst at Guidehouse, tells Inverse.
Chavez noted that Tesla and other firms have announced plans to develop batteries with less lithium, nickel, and cobalt. Musk announced plans in June 2018 to ditch cobalt entirely, a material mainly sourced from the Democratic Republic of the Congo in terrible conditions. A Battery Day event scheduled for April is expected to detail the company’s plans for future technologies in more detail.
A Tesla car charging.
“The industry is moving toward formulations that replace up to 90 percent of that cobalt with other metals like nickel and manganese, both of which are more readily available,” James McKone, assistant professor at the University of Pittsburgh’s department of chemical and petroleum engineering, tells Inverse. “As an added benefit, these ‘low-cobalt’ electrodes can also be made to deliver more energy in the same package. The real challenge, though, will be eliminating cobalt entirely, which may require a more significant rethinking of the basic chemical formulations in these batteries.”
But the main reason why Tesla doesn’t have enough batteries may be simpler than access to materials or chemical composition – it could be because they don’t produce enough.
“I think it’s more to do with actual lack of battery manufacturing capacity than an issue with lithium supply,” Calum MacRae, automotive analyst at GlobalData, tells Inverse.
Considering how quickly the company has expanded, that’s perhaps not surprising. Tesla has produced around 900,000 cars since its founding, more than two-thirds of which were produced after the entry-level Model 3 entered production in July 2017. These cars need batteries that can reach up to 100 kilowatt-hours.
Tesla has been part of the mass expansion of the electric car market. The number of electric cars on the world’s roads has soared from just over 700,000 in 2015 to 3.3 million in 2018.
Tesla’s battery production has been gradually increasing. In August 2018, Tesla announced it had reached a production rate of 20 gigawatt-hours per year at the Nevada Gigafactory, more than every other automaker combined. During Tesla’s July 2019 earnings call, Musk revealed that the company was producing around 35 gigawatt-hours worth of batteries annually.
But Tesla wants more, and Musk has spoken of his ambition to reach the terawatt-hour scale. That’s far beyond total global capacity. Wood Mackenzie claims total global manufacturing capacity reached 285 gigawatt-hours by November 2019, and is set to reach 777 gigawatt-hours by 2026.
“There are lots of Gigafactories for lithium-ion batteries in the planning but few outside China,” MacRae says, also noting how Tesla’s Nevada factory has yet to reach its planned full capacity. “Tesla’s other problem is that it is competing with, in the main, with two other cohorts – established [original equipment manufacturers] now looking to electrify their fleets and Chinese OEMs riding the [new energy vehicle] wave in China – that are all on the increase.”
That’s led to a number of agreements to grab at some of that much-needed supply. Tesla has worked with Panasonic as its long-time battery partner, but Reuters reported that the company has partnered with China’s CATL and South Korea’s LG Chem to supply even more batteries.
CATL's facilities.
“I think it’s a question of supply catching up with burgeoning demand,” MacRae says. “Of course what effect this burgeoning demand will then have on lithium prices and end battery costs is another bridge that the industry has to cross.”
Once we reach that stage, it could change the conversation around battery production. The UK Energy Research Centre stated in March 2018 that it’s unclear how much lithium is in the planet. While one 2008 story placed the figure at 3.9 million tons, a 2010 study placed the figure over 10 times higher. Bloomberg New Energy Finance declared in September 2017 that the next dozen years will only deplete around one percent of total global lithium stores – with the main bottleneck in whether there will be enough mines to meet demand.
“There have certainly been concerns raised over the long-term supplies of lithium and cobalt, but there is much more research emphasis on reducing or eliminating cobalt,” McKone says. “Replacing lithium with another element (like sodium or magnesium or aluminum) is also under active investigation by research labs across the world, but that transition is much further out, and it’s not clear whether it will even be necessary.”
While Tesla’s main headache today is whether it can build enough batteries, the headaches of the future may look completely different.