We're drowning in a sea of plastic. A new process could be a life preserver
Before you put your grocery bags into the recycling, read this.
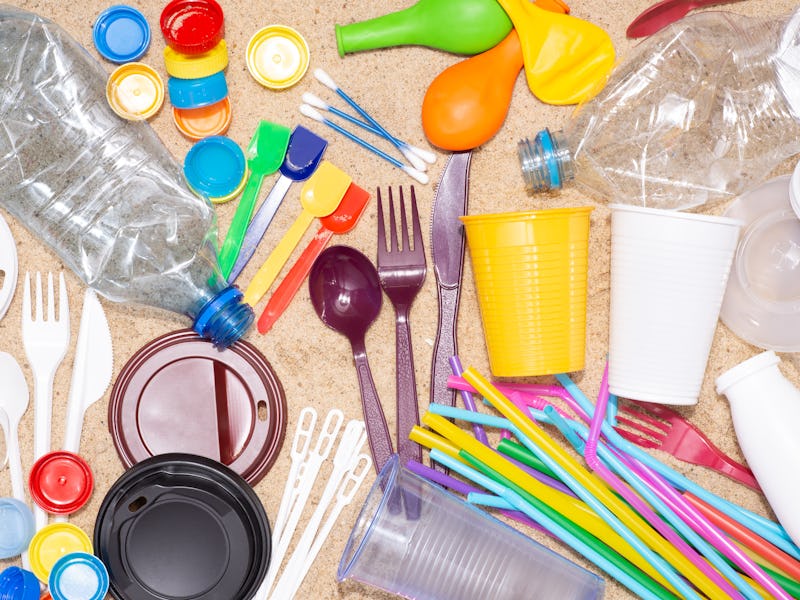
Milk jugs, bags, egg cartons, water bottles — Americans use a lot of plastic packaging.
According to the most recent numbers from the Environmental Protection Agency (EPA), Americans generated 14.5 million tons of plastic containers and packaging waste in 2018, comprising around 5 percent of total waste that year.
The burden of plastics is not helped by the fact that so few of them get recycled. In that same year, 2018, a paltry 8.5 percent of plastics were recycled. Scientists are working frantically to produce a better material to take plastics' places in our lives, but until that happens, it seems we're stuck with them. But that doesn't mean we need to stick with that shocking recycling statistic.
New advances from a team at the University of Madison-Wisconsin could hold the key.
The researchers have created a technique called STRAP, or Solvent-Targeted Recovery and Precipitation processing, that could be the answer to our recycling problem. In a study published Friday in the journal Science Advances, the researchers lay out their case for why the technique could start a recycling revolution.
We know what you are thinking: Plastics are recyclable. But the reality is actually much more complicated. There are six major forms of plastic that a person is likely to encounter on a daily basis: polystyrene (think meat packaging), low-density polyethylene (garbage bags), polypropylene (Tic-tac boxes), polyvinyl chloride (juice boxes), high-density polyethylene (plastic crates), and polyethylene terephthalate (soda bottles).
Bags of potato chips are more complicated than they appear.
All of them wind up in recycling bins across the U.S. But here's the catch: Only the last three are actually recyclable. Polyethylene, which makes up garbage bags, potato chip bags, cable insulation, and more, has a surprisingly complex structure. While a bag of chips might not look very complex on the outside, it is in fact a multi-layered plastic bag. Polyethylene is made up of several extremely thin films stacked on top of each other to provide strength, flexibility, and integrity. That is why you can't smell the barbecue chips from the outside of the bag.
The multi-layer approach does its job, but it comes with a cost. The layers are chemically incompatible when it comes to breaking them down. They simply cannot be recycled en masse like soda bottles can.
That is where the new technique comes in.
The STRAP process
The key to the new process is to “selectively dissolve a single polymer layer in a solvent system in which the targeted polymer layer is soluble, but the other polymer layers are not," according to the paper. In other words, you need to break down each polymer layer individually, and use a solvent to dissolve them one at a time.
The team tested their process using a real-world multilayer film built by Amcor Flexibles, which designs pouches and bags for food, drinks, healthcare, and other essentials.
The process "achieved separation of these three components with nearly 100 percent material efficiency,” according to the paper.
George Huber, a co-author of the study, says the STRAP process could eventually level up to take on current levels of plastic waste.
“All the equipment we used is very standard in chemical processing, so this process should be very easy to scale up with existing chemical engineering tools,” he said in a press statement.
But “should” does not mean it can achieve this goal any day soon. Modern recycling plants typically rely on mechanical recycling, as opposed to the chemical techniques the team proposes in this paper.
“Our approach will require current plastic recyclers to understand how to do chemical processing of plastics,” Huber says.
This caveat highlights an inconvenient truth of innovations to plastics and their disposal — coming up with new ways to produce "clean" plastics and to dispose of them in a way that does no harm is perhaps easier than actually putting these inventions and strategies into practice.
ABSTRACT: Many plastic packaging materials manufactured today are composites made of distinct polymer layers (i.e., multi-layer films). Billions of pounds of these multilayer films are produced annually, but manufacturing inefficiencies result in large, corresponding postindustrial waste streams. Although relatively clean (as opposed to municipal wastes) and of near-constant composition, no commercially practiced technologies exist to fully deconstruct postindustrial multilayer film wastes into pure, recyclable polymers. Here, we demonstrate a unique strategy we call solvent-targeted recovery and precipitation (STRAP) to deconstruct multilayer films into their constituent resins using a series of solvent washes that are guided by thermodynamic calculations of polymer solubility. We show that the STRAP process is able to separate three representative polymers (polyethylene, ethylene vinyl alcohol, and polyethylene terephthalate) from a commercially available multilayer film with nearly 100% material efficiency, affording recyclable resins that are cost-competitive with the corresponding virgin materials
This article was originally published on