New discovery may shape the future of construction on Earth and Mars
3D printing is green. This new method makes it even greener.
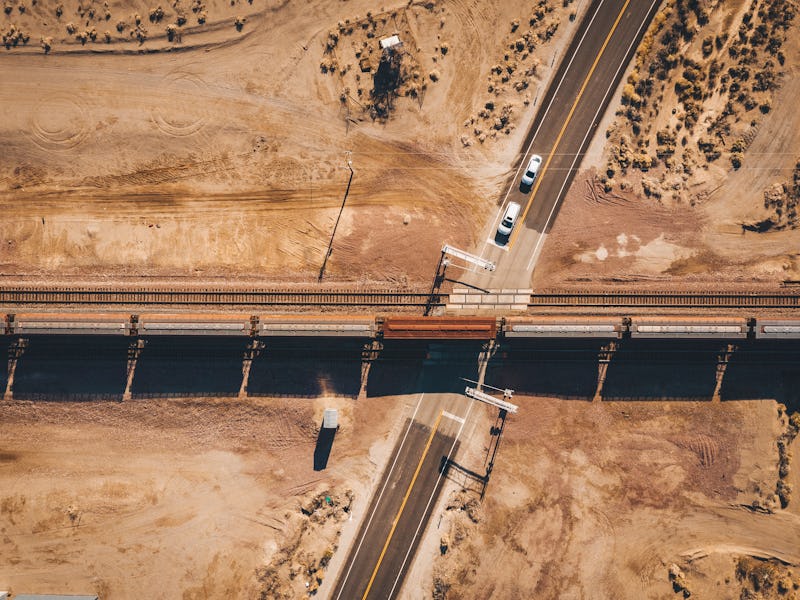
The construction industry is due for a green revolution. For years, it's been marked as one of the key challenge areas when it comes to mitigating the climate crisis, with the target pointed at construction materials. On its own, cement creates around 8 percent of the world’s carbon dioxide emissions, according to the thinktank Chatham House.
3D printing has been hailed as a way construction could mitigate its contributions to global warming, with materials being made in labs using fewer materials, less processing energy, and weighing lighter during transport. It’s a clear improvement over Portland cement, but it still has a footprint of its own.
That’s where a new technique from Texas A&M University comes into play. It allows for the creation of building materials out of local soil.
The small structure made out of a colleague's backyard soil.
Aayushi Bajpayee, a graduate student who worked on the project, tells Inverse that the project harkens back to the earliest days of construction.
"Historically, humans used to build with locally sourced materials, such as adobe, but the move to concrete has raised many environmental issues. Our thought was to turn the clock back and find a way to adapt materials from our own backyards as a potential replacement for concrete," Bajpayee explains.
Presenting this week at the American Chemical Society Fall 2020 Virtual Meeting & Expo with project principal investigator Sarbajit Banerjee, Bajpayee and her team looked beneath the surface for the project.
It starts with clay, which is at varying depths below surface dirt. Using clay they found in a colleague’s backyard, the team mixed with the material with an environmentally friendly additive. Using the new mixture, the researchers created tiny structures — cubes measuring two inches on each side — and stacked them into layers.
The stacks stuck — but buildings have to do more than just stand up straight. They also have to carry weight, what’s known as “load-bearing.” A building's weight includes everything from the floors and equipment inside a building to the insulation in its walls. Load-bearing abilities are just as crucial to a building as its ability to stand up
For that, the team turned a technique known as “zippering,” which allowed them to prevent water absorption on a microscopic layer.
This process was a challenging one, Bajpayee admits.
“Turning backyard clay into a printable formulation required the considerable design of the chemistry — we had to make sure that the formulation did not set too rapidly, since that would clog the nozzle, or too slowly-since that would make it impossible to put down the next layer.
We also spent a lot of time designing a zipper that was naturally sourced and that would not present toxicity concerns — since one of the key advantages of 3D printed buildings is the ability to tear them down and recycle them at the end of their operational life,” she says.
The time spent on this process paid off: the material could hold twice as much weight as the unmodified clay mixture.
What's next — Improving on that doubling is the team’s next priority. They’ll continue to work on improving the material’s load-bearing capacity, which they feel could be used in nearly any construction capability.
The team thinks that its process could be eventually used in nearly any construction scenario, even ones in cities or, in the far off, future, a city on Mars.
While getting enough natural clay in an urban environment would be “challenging,” Bajpayee tells Inverse, “the overall environmental impact of procuring soil and bringing it to an urban center is still generally much lower than using concrete." She also notes that the "tighter spaces in urban environments also make 3D printing attractive for being able to design custom structures that fit in with the architecture of the surroundings.”
Bajpayee thinks this material could be especially useful for “low-cost dignified habitats,” with the potential to create affordable housing where none exists. Hopefully, someone wouldn’t have to go to Mars to get that.
Abstract: The construction industry is being buffeted by winds of change, balancing the urgent need to remedy deteriorating infrastructure in the developed world and the push to build new infrastructure in emerging economies whilst devising means to better its catastrophic carbon footprint and inefficiencies across the construction process that result in considerable waste and energy expenditure. Additive manufacturing methods stand out to transform the industry by enhancing automation, however, reliance on concrete as the extrusive material of choice has the potential to compound mounting environmental challenges. We discuss our efforts to develop a new palette of naturally sourced construction materials based on natural soils, which are reconfigured into extrudable formulations compatible with additive manufacturing. We delineate a roadmap bringing together soil chemistry with composite science, modeling of mesoscale phenomena, rheological studies of extrudable soil inks, generative design, and the development of robust structure--function correlations relating atomistic and mesoscale structures as well as geometry of the architectures to load-bearing capabilities. We illustrate this approach using a naturally harvested burlewash clay sample crosslinked through formation of a siloxane framework which has been 3D printed into a load-bearing structure. The need for an integrated life cycle assessment approach is emphasized to ensure development of a new palette of sustainable construction materials.
This article was originally published on