A Skull Drill Could Be the Savior for Brain Surgery
Capable of slashing one cranial procedure from two hours to two-and-a-half minutes.
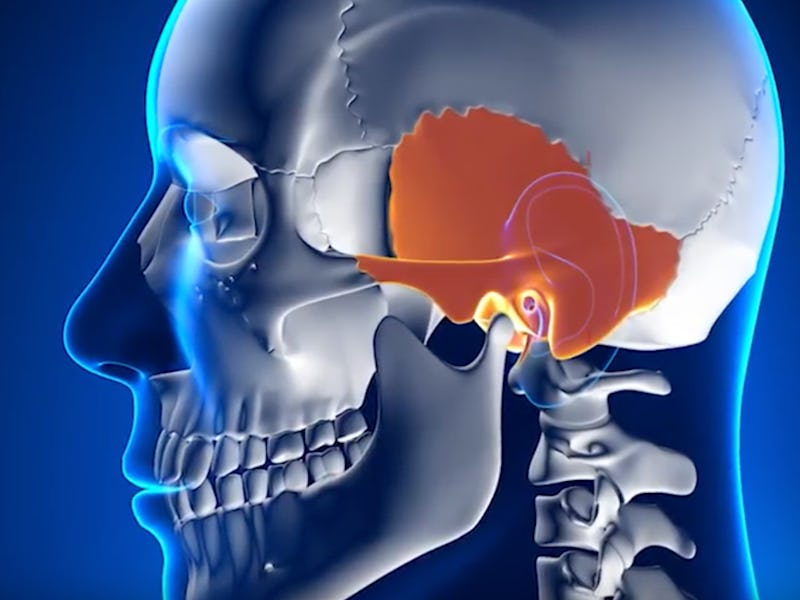
Few things are as complicated as surgery, and one of them is definitely brain surgery. Cracking through the skull and cutting right into what is arguably the most important organ in the body is fraught with risk. A single human error could quickly diminish one’s ability to think intelligently, function independently, and live a long, healthy life.
Would you feel better about potentially putting a robot in the driver’s seat? You should.
That’s the idea behind a new kind of computer-controlled drill developed by medical researchers at the University of Utah Health. Biomedical researchers recently created an automated drill inspired by machine auto parts which are able to accelerate a type of complex cranial surgery up to 50 times faster than through standard manual methods. This specific procedure’s length of time is slashed from over two hours to just two-and-a-half minutes, according to results published Monday in the journal Neurosurgical Focus.
In the past, brain surgeons manually operated drills to carve out specific, elaborate openings through the skull to provide access to the brain. Structures had to be removed carefully and precisely, with almost no margin for error.
A robotic drill, on the other hand, can move with a much higher rate of precision and accuracy. No need to worry about a shaky hand. No need to worry about accidentally drilling too far.
“Machines, when designed correctly and well, do not get tired or fatigued and are capable of performing repetitive tasks consistently and well,” lead researcher Dr. William Couldwell tells Inverse. “You do need to inform the machine what it is supposed to do very explicitly. The surgeon is still involved with the surgery, but for a tedious job like bone removal, the machine takes over and does the preliminary tasks quickly, thus allowing the surgeon to focus on other later aspects of the surgery with greater efficiency and reduced fatigue.”
Couldwell brought together a team of medical researchers and engineers to build, test, and improve the drill. Although the engineering side was more used to developing equipment meant to slice through metal, the team managed to fine-tune a softer tool that didn’t tear up the skull and brain matter behind it.
“Of primary importance was the need to develop a safe and reliable device, capable of ensuring repeatability,” says Couldwell. “Also of importance was the need to have a device that could provide access to the surgeon during the surgery. The design team also considered the need for portability of the drill so that it could be easily transported into an operating room.” The whole thing was conceived as a low-cost tool which could intensely expedite the time and resources put into cranial surgeries.
In a typical procedure involving the new drill, the patient is first imaged through a CT scan to collect data relevant to the size and position of the skull and the location of sensitive parts like nerves, arteries, and veins. A special software designed by the team analyzes the data to provide a set of options about where to best drill — sort of the way navigation software on smartphones list out options depending on the user’s preferences. The surgeon can apply safety modifications on the drilling path that will avoid special barriers within a single millimeter. Essentially, the drill will slow down as it begins to navigate around these barriers — Couldwell refers to them as “no-fly zones” — and stop short of breaching the boundaries.
Then, the drill simply has to do its work on the operating table, making specific holes that remove the bone around the brain to allow surgeons to pick off entire parts. Couldwell and his team tested the drill out specifically on the translabyrinthine opening — a jigsaw-like shape around the ear intricately lined with strangely shaped, hard bone. For Couldwell, demonstrating that the drill could successfully carve through this kind of bone was a robust proof of concept to support the efficacy and safety of the drill.
And when there is an increased risk the drill might damage sensitive tissue, an emergency shut-off switch kicks in automatically, as a response to problems detected in facial nerves.
A shorter drilling procedure won’t just increase the amount of time and energy surgeons can devote to the rest of the surgery. It should also lower chances of infection and improve post-op recovery since it shortens the amount of time patients must remain in a state of vulnerability.
Couldwell expect the drill can be easily applied to other surgical procedures relevant to other body parts as well. “Other cranial openings could be performed by the drill- through the skull or face,” he says. “In addition, drilling of the spine or joints for placement of hardware for spinal fusion, or machining bone to receive artificial joints, could also be performed.” It’s just a matter of testing the drill out and fine tuning it so it’s suitable for these operations.
Regardless, it’s clear that surgery, like much of medicine, is quickly moving into a realm where automated technology can handle the bulk of the rote work so that surgeons can focus more of their mental stamina on problem- solving during operations. If there’s a fear about how badly a robot could err during surgery, it’s probably worth remembering that human error manifests much more frequently, and often with more problematic consequences.